
The Indian space agency ISRO developed a lunar soil simulant and terrain to test their Chandrayaan landers and rovers. For example, ESA created the Wide Range Test Facility to test their upcoming JUICE spacecraft’s ability to survive temperatures as low as -230 degrees Celsius (-382 degrees Fahrenheit), which is what it can experience when Jupiter or its moons eclipse the Sun. Many times entirely new facilities have been created for cutting-edge missions. These include specialized antenna testing for communications, optical testing for cameras and telescopes, helicopter-based radar testing for missions studying subsurfaces of planets and moons, deployment mechanism tests for space telescopes like JWST, heat shield and parachute testing for Mars landing missions and crew capsules returning to Earth, and more. It also has large 15-meter (49-foot) coils to offset Earth's magnetic field to ease spacecraft testing.Īdditional tests for each spacecraft can vary as greatly as the missions themselves. ESA’s IABG has one such remote test facility, which avoids interference from civilization-generated magnetic fields thanks to its location in a forest and the fact that it's made of non-magnetic materials such as wood. Likewise, spacecraft that will study magnetic fields - such as those of Earth, the Sun or Jupiter - are placed in special chambers to ensure magnetic noises from their instruments are contained. Faraday Cage chambers, which have foamy interiors to block outside electromagnetic radiation, are used to understand a spacecraft’s own electrical and radio noises, and ensure they don't interfere with each other and affect scientific observations or damage onboard electronics. There are also tests to prevent a spacecraft’s own instrument noises from ruining the mission.
SPACESHIP IN SPACE SOFTWARE
For example, NASA tested the Perseverance rover’s navigation and landing software over seven years, starting with it running on Mars rover computer models, followed by mission-relevant sensors, and lastly on actual Mars-bound hardware. Since terrestrial electronics don’t (reliably) work in harsh space environments, spacecraft computers are built using hardened components tested in more than 100 ways to reduce radiation and mechanical damage.Įach spacecraft’s software is also tested rigorously, because while it can be patched post-launch, the extent is limited. NASA’s Space Power Facility at the Glenn Research Center's Space Environments Complex is the world’s largest vacuum chamber, and has been used to test not just spacecraft but also rocket fairing separations, Mars landing systems, solar array deployments, and much more. ESA’s HYDRA facility can generate vibrations equivalent to an earthquake of 7.5 on the Richter scale. For this, all spacecraft - and sometimes even their individual components - are tested pre-launch on electric or hydraulic shaker tables, which simulate a rocket’s intense vibrations. The chamber has large stereo-speaker-like noise horns that simulate launch sounds while noise absorption coatings sustain the noise and cause reverberations.Ī spacecraft’s structure also needs to survive the jolt from rocket engines turning on and the vibrations they generate during flight. To ensure this, spacecraft are tested before launch in special acoustic chambers, like the European Space Agency’s (ESA) Large European Acoustic Facility. A spacecraft sitting on top of a rocket needs to avoid mechanical damage from this intense, sustained acoustic noise.
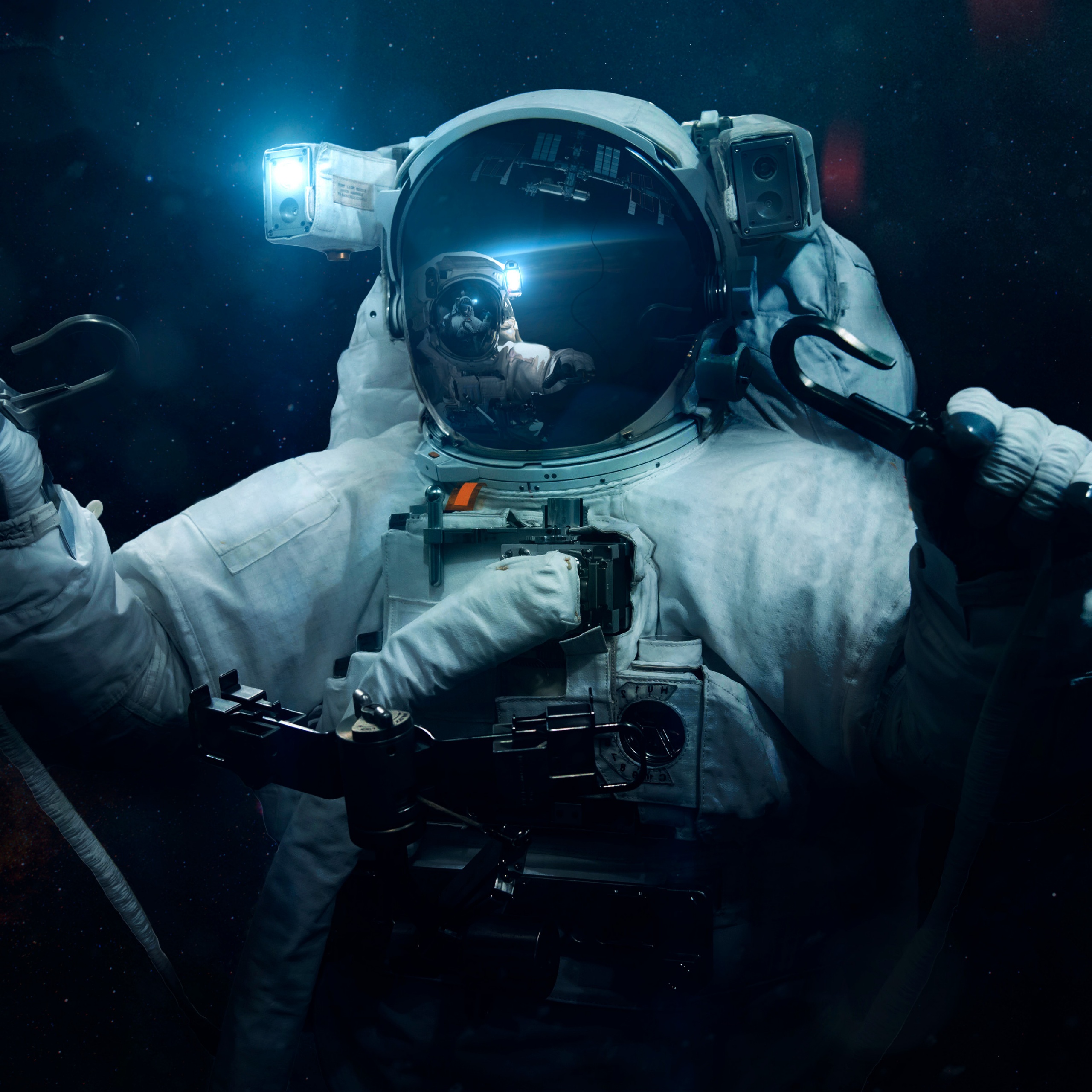
Launch testingĪnyone who has seen a rocket launch in person ( I have!) knows how noisy rockets are, the rumbles of which can be heard across great distances. To ensure these orchestrate in the harshness of space, where fixing major issues post-launch is either impossible or limited in scope, every spacecraft is extensively tested in facilities that mimic mission conditions. Hundreds to thousands of experts from several distinct fields come together to build the thousands of parts and functions of a spacecraft. A space mission is an immensely complex undertaking.
